Fokus auf Wertschöpfung
So erkennen und beseitigen Sie
Verschwendung in Ihrem Unternehmen
– Ein Plädoyer für den Fokus auf Wertschöpfung,
Effizienz und Produktivität –
Möchten Sie Ihre Geschäftsprozesse effizienter und wirtschaftlicher gestalten? Den Fokus nachhaltig auf die Wertschöpfung legen? Oder in Zukunft Ihre Geschäftsprozesse digitalisieren?
Dann zeige ich Ihnen, wie Sie Verschwendung in Ihren Prozessen erkennen und beseitigen können. Anschließend werden Sie nicht nur mit Hilfe der Methoden des Lean Managements die einzelnen Verschwendungsarten beseitigen, sondern auch Dank schlanker Produktionssysteme schnell und flexibel auf neue Herausforderungen Ihrer Kunden und Märkte reagieren können.
So können Sie in Zukunft Verbesserungspotentiale erkennen, Ihre Produktivität steigern, Ihre verfügbaren Ressourcen schonen und damit in Summe auch Ihre Kosten reduzieren.
Verschwendung, Wertschöpfung und die drei Mu‘s
Wer kennt das nicht aus seiner eigenen Produktion, Logistik und Verwaltung: Man sieht, dass manche Prozesse nicht richtig funktionieren, aber man bekommt die Probleme einfach nicht in den Griff.
Ein wirksames Mittel zum Optimieren der Prozesse und zum Aufbau eines funktionierenden, schlanken Produktionssystems ist es, die Verschwendung (Muda) in den Prozessen zu beseitigen. Aber was ist nun Verschwendung genau? Vereinfacht gesagt ist alles, was nicht der Wertsteigerung dient, Verschwendung.
Die meisten von uns haben bestimmt schon von den verschiedenen Verschwendungsarten gehört. Trotzdem ist es wichtig, sich die einzelnen Verschwendungsarten immer wieder vor Augen zu führen, aber auch immer wieder zu rekapitulieren, wie das richtige Vorgehen zu ihrer Beseitigung aussieht.
Überblick über die acht Verschwendungsarten

Mit dem Laden des Videos akzeptieren Sie die Datenschutzerklärung von YouTube.
Mehr erfahren
Die Verschwendungen zu beseitigen, ist der erste Schritt auf dem Weg zum Erfolg. Am einfachsten geschieht dies mit den Methoden des Lean Managements. Zur wirkungsvollen Anwendung der Methoden des Lean Managements wurden von Toyota sieben Verschwendungsarten in Geschäfts- oder Produktionsprozessen identifiziert, die wir im Folgenden ausführlich beschreiben. Zusätzlich werden bekannte Methoden des Lean Managements aufgeführt, mit denen die einzelnen Verschwendungsarten beseitigt werden können.
Sie lassen sich auf die Produktentwicklung, die Auftragsannahme und administrative Tätigkeiten genauso anwenden, wie auf die direkte Fertigung und Logistik. Es gibt außerdem die achte Verschwendungsart „Ungenutzte Mitarbeiterpotentiale“, die wir hier mit aufgenommen haben. Letztendlich führt die konsequente Beseitigung von Verschwendung zu einer Steigerung ihrer Produktivität, zur Schonung der ihnen zur Verfügung stehenden Ressourcen und damit in Summe auch zu einer Reduzierung ihrer Kosten.
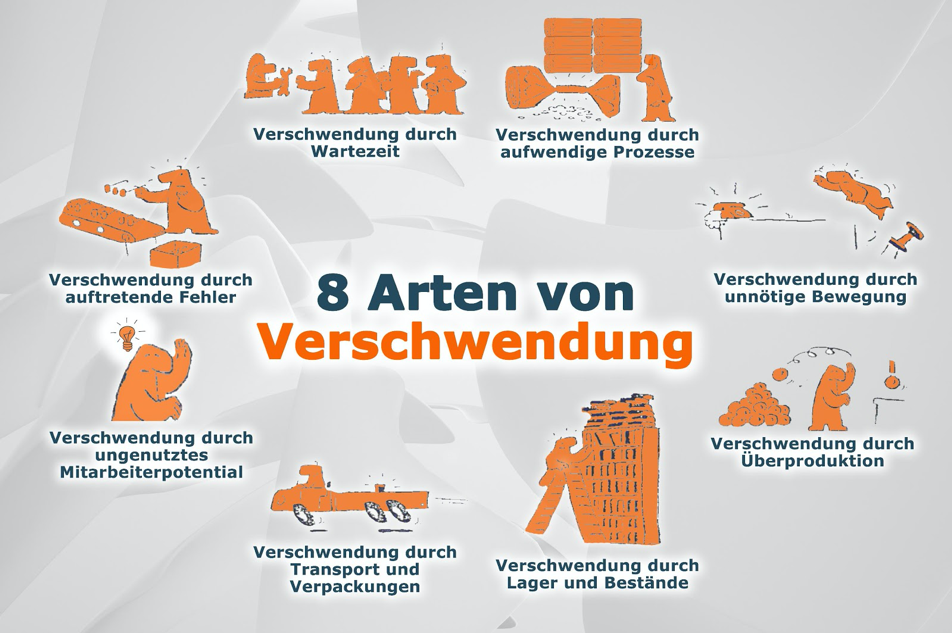
Zur nachhaltigen Eliminierung der Verschwendung in den Produktions-, Logistik-, Entwicklungs- und Verwaltungsprozessen müssen die folgenden fünf Punkte unbedingt beachtet werden:
- Tiefes Verständnis und Erfahrung bei der Anwendung der Methoden des Lean Managements
- Genaues Identifizieren der Verschwendung
- Detailliertes Herausarbeiten der Ursachen für die Verschwendung
- Zielgerichtetes Vorgehen bei der Beseitigung der Verschwendung
- Kontinuierliche Verbesserung der optimierten Prozesse
1. Auftretende Fehler
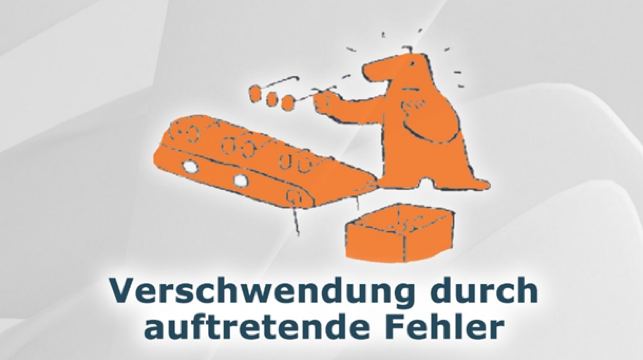
Die Produktion fehlerhafter Teile beziehungsweise deren Nachbesserung, Reparatur, Ausschuss, Neuproduktion und Überprüfung sind keine wertschöpfenden Aktivitäten und somit eine Verschwendung von Handgriffen, Zeit, Geld und Energie.
Genauso müssen auftretende Fehler an Maschinen und Anlagen vermieden werden, da sie die zur Verfügung stehende Anlagenkapazität reduzieren und im schlimmsten Fall zu Ausschuss im Produktionsprozess führen.
Mit Hilfe von z.B. Qualitätsmanagement-Systemen, TPM (Total Productive Maintenance), robusten Prozessen, Prozessanalysen und den bekannten Methoden der Problemlösung lassen sich auftretende Fehler verringern bzw. im besten Fall vollständig vermeiden.
2. Wartezeit
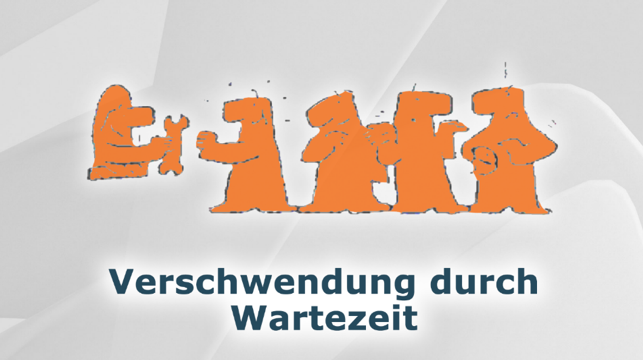
Wartezeit entsteht z.B. dann, wenn Arbeiter nur dazu eingesetzt werden, die Maschinen zu überwachen, oder wenn sie auf den nächsten Schritt der Weiterverarbeitung, auf Werkzeuge, Materialnachschub, Teile, etc. warten müssen. Das gleiche gilt auch dann, wenn Arbeiter einfach nichts zu tun haben, weil der Nachschub stockt oder sie auf notwendige Informationen warten. Dann verursacht die Wartezeit Verzögerungen im Fertigungs- oder Logistikprozess sowie eine mangelnde Auslastung der Maschinen und kann im schlimmsten Fall zu Kapazitätsengpässen führen.
Um die Wartezeit zu verringern, können verschiedene effiziente Methoden des Lean Managements, wie z.B. Prozessbeobachtung, Fließfertigung, Mehrmaschinenbedienung und Schnellrüsten angewandt werden.
3. Aufwendige Prozesse

Eine weitere wichtige Verschwendungsart sind aufwendige Prozesse in der Fertigung, im Entwicklungsprozess oder auch in der gesamten Wertschöpfungskette. Dies können z.B. unnötige Prozessschritte in der Verarbeitung, zu hoher Materialeinsatz oder auch schlecht abgestimmte Lieferprozesse mit Lieferanten sein.
Ineffiziente Prozesse können auch das Ergebnis des Einsatzes ungeeigneter oder überdimensionierter Anlagen und Werkzeuge sein. Aber auch ein schlechtes oder nur ungenügend an die Kundenanforderungen angepasstes Produktdesign kann zu unnötigem Aufwand und Mängel führen. Auch die Herstellung von Produkten mit einer höheren Qualität als erforderlich ist eine Form der Verschwendung. Manchmal wird auch unnötige Zusatzarbeit verrichtet, z.B. um Leerläufe zu füllen. In diese Kategorie fallen auch übermäßig viele Testschritte während der Produktion, damit die Produktqualität sichergestellt werden kann.
Mit den Methoden der Wertstromanalyse und der Prozessoptimierung sowie auch mit kontinuierlichem KAIZEN können aufwendige Prozesse identifiziert und optimiert werden. Für die Überprüfung des Produktdesigns ist die Methode der Wertanalyse sehr gut geeignet.
4. Unnötige Bewegung
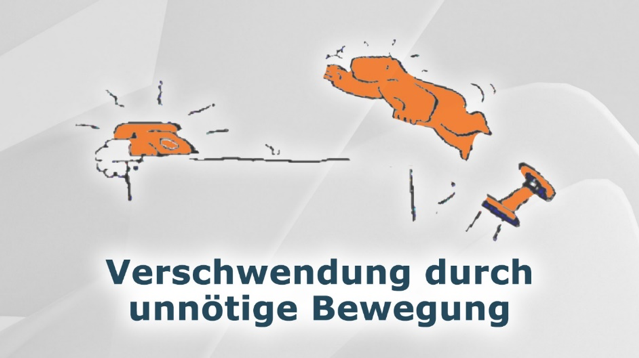
Jede überflüssige Bewegung, die ein Mitarbeiter bei der Durchführung seiner Arbeit machen muss, um zum Beispiel Teile und Werkzeuge zu suchen oder zu holen oder sich Informationen zu beschaffen, ist Verschwendung. Hierzu zählt auch die Suche nach Material oder weite Wege zwischen den einzelnen Fertigungsschritten. Auch nicht ergonomisch ausgeführte Arbeitsplätze mit langen Greifwegen oder Arbeitsplätze ohne Montagevorrichtungen sind der Auslöser für unnötige Bewegungen.
Zur Identifizierung unnötiger Bewegungen kann die Methode der Prozessbeobachtung oder die visuelle Darstellung von Laufwegen in einem Spaghetti-Diagramm angewandt werden. Zur Vermeidung unnötiger Bewegungen müssen Arbeitsplätze ergonomisch nach dem Best-Point-Prinzip ausgeführt werden. Auch Fließfertigung und der Aufbau von Fertigungsanlagen nach dem One-Piece-Flow Prinzip führen zu einer signifikanten Reduzierung von unnötigen Bewegungen.
5. Überproduktion
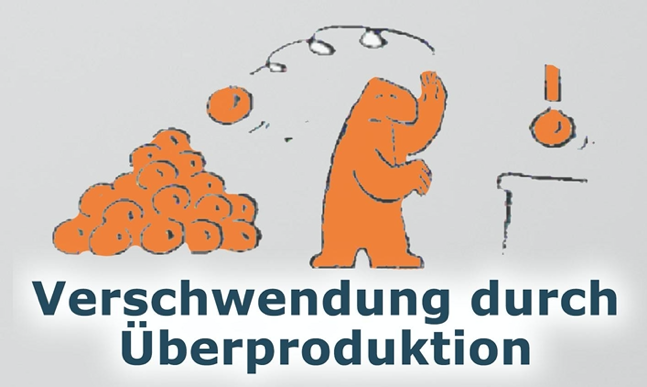
Verschwendung durch Überproduktion ist eine der schlimmsten Arten von Verschwendung, die man allgemein in den Unternehmen findet. Diese Verschwendung entsteht dann, wenn Waren ohne Bestellung oder über den Bedarf des Marktes hinaus produziert werden. Überproduktion führt zur Verschwendung von Arbeitskraft, zu großen Lagerbeständen und zu hohen Bestands-, Lager- und Transportkosten.
Da Überproduktion häufig auch noch grundlegendere Probleme verschleiert, sollte man sie unbedingt beseitigen. Zudem führen übergroße Bestände nur zu Verwirrung bei der Frage, was als nächstes getan werden muss. Die Mitarbeiter werden verunsichert und davon abgelenkt, sich auf ihre augenblicklichen Aufgaben und Ziele zu konzentrieren.
Der Aufbau einer Produktion als Fließfertigung und die Einführung von bedarfsgesteuerten KANBAN-Regelkreisen sind erste Schritte, um Überproduktion zu vermeiden. Zusätzliches Nivellieren und Glätten in der Produktion führt zu kleinen Losgrößen und macht in letzter Konsequenz weitere Verschwendung sichtbar.
6. Lager und Bestände

Ein zu großer Bestand an Rohmaterialien, Ware in Arbeit und Endprodukten führt zu längeren Durchlaufzeiten und zu veralteten oder sogar beschädigten Teilen sowie zu hohen Transport- und Lagerkosten und zu Verzögerungen im Produktionsablauf. Viele Lager und hohe Bestände führen außerdem zu einem großen Flächenbedarf. Hohe Bestände verschleiern außerdem Probleme, wie eine unausgeglichene Produktionsauslastung, eine verspätete Materialzulieferung, Störungen und Fehler an den Produktionsanlagen, Maschinenleerläufe sowie lange Einrichtungs- und Umrüstzeiten.
Neben den bei der Überproduktion angewandten Methoden des Lean Managements können Lager und Bestände durch die Anwendung von Schnellrüsten sowie durch den Einsatz von Supermärkten signifikant reduziert werden.
7. Transport und Verpackung
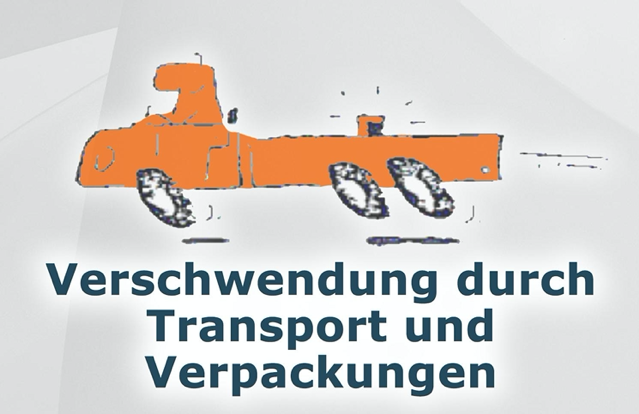
Verschwendung durch Transport und die unnötige Handhabung von Teilen im Produktionsprozess zählen zu den am häufigsten auftretenden Verschwendungsarten in der Produktion. Dazu zählt auch der häufige Transport von Rohmaterial, Ware in Arbeit oder Endprodukten zur Zwischenlagerung oder Weiterverarbeitung selbst über kurze Entfernungen. Ein falsch geplantes Hallenlayout führt unter Umständen ebenfalls zu langen Transportwegen. Genaue Analysen zeigen, wie viele Kilometer ein Werkstück durch die Fabrik transportiert wird, bevor es fertiggestellt ist. Überdimensionierte Verpackungen, die zeitaufwendig befüllt werden oder Verpackungen, die nur mit großem Aufwand geöffnet werden können, zählen ebenfalls zu dieser Verschwendungsart.
Um diese Verschwendung auszuschalten, müssen Verbesserungen sowohl in Bezug auf die Anordnung der Betriebsmittel als auch hinsichtlich Fertigungssteuerung, Transportmethoden und Arbeitsplatzorganisation in Betracht gezogen werden. Prozessbeobachtungen und Materialflussanalysen helfen, z.B. durch den Einsatz eines Spaghetti-Diagrammes, diese Verschwendungsart sichtbar zu machen. Auch die Einführung von Fließfertigung, Supermarktsystemen und Routenzügen führt häufig zu einer signifikanten Reduzierung der Transport- und Handhabungsvorgänge.
8. Ungenutze Mitarbeiterpotentiale
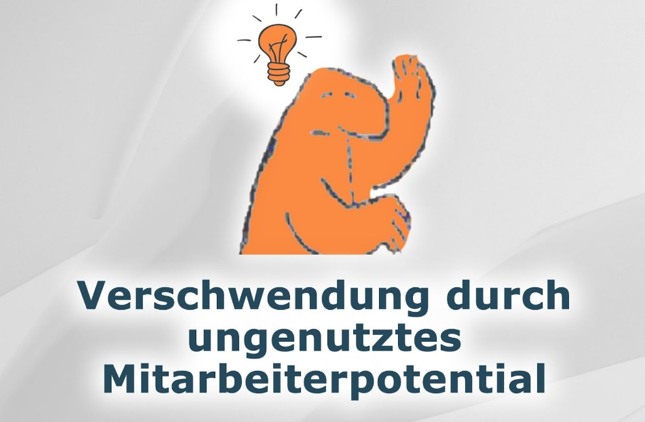
Neben den sieben klassischen Verschwendungsarten wird mittlerweile sehr oft eine achte Verschwendungsart genannt. Dabei handelt es sich um ungenutzte Mitarbeiterpotenziale. Ungenutzte Mitarbeiterpotenziale führen zu Frustrationen bei den Mitarbeitern und zu einem Verlust an Zeit, Ideen und Verbesserungen, weil die Mitarbeiter kein Gehör finden oder sie nicht in den Verbesserungsprozess einbezogen werden.
Diese Verschwendungsart entsteht häufig, wenn Führungskräfte das Potenzial ihrer Mitarbeiter nicht erkennen und nutzen. Um dies zu vermeiden, müssen Führungskräfte umfassend geschult sein, als gutes Beispiel vorangehen und die vorgegebenen Maßnahmen einfordern.
Mit regelmäßigen KAIZEN Aktivitäten zur kontinuierlichen Verbesserung der betrieblichen Abläufe oder durch regelmäßiges Shopfloor-Management direkt am Ort des Geschehens können Führungskräfte die Erfahrungen und das Wissen ihrer Mitarbeiter gezielt nutzen und in den Verbesserungsprozess mit einbinden. Das Ziel ist es dabei, bestehende Probleme aufzudecken und dann mit den betroffenen und beteiligten Mitarbeitern in einem strukturierten Problemlösungsprozess die Ursachen zu erforschen und Lösungen für nachhaltige Abstell- und Verbesserungsmaßnahmen zu entwickeln.
Eliminierung der drei „Mu’s“
Ein wichtiger Grundsatz von Lean Management ist jedoch nicht nur die Vermeidung der Verschwendung Muda, sondern die Vermeidung und Eliminierung aller drei “Mu‘s”, also auch von Muri und Mura, wie sie in KAIZEN definiert sind.
Muri (Überbelastung)
„Muri“ steht für Überbeanspruchung. Es handelt sich hierbei um Verluste, die durch Überlastung (z.B. Stress, Übermüdung, Anlagenfehlplanung) während des Arbeitsprozesses entstehen. Es wird zwischen einer Überbelastung von Mitarbeitern und Führungskräften sowie einer Überlastung von Maschinen und Herstellprozessen unterschieden.
Es handelt sich dabei bei Mitarbeitern und Führungskräften um körperliche und geistige Überbeanspruchung, die sich in Form von Übermüdung, Stress, Fehlerhäufigkeit und Arbeitsunzufriedenheit äußern kann. Auch im Herstellungsprozess treten Überlastungen auf, die durch mangelnde Harmonisierung des Produktionsflusses oder durch Planungsfehler auftreten.
Mura (Unausgeglichenheit)
Die Unausgeglichenheit, auch „Mura“ genannt, steht für Verluste durch fehlende oder nicht vollkommene Harmonisierung der Kapazitäten bei der Fertigungssteuerung. Verluste im Sinne von Mura können durch Warteschlangenbildung oder durch nicht optimal ausgelastete Kapazitäten, also z.B. durch nicht prozessbedingte Leerzeiten, entstehen.
Muda (Verschwendung)
„Muda“ bezeichnet die Vermeidung von Verschwendung und nicht werthaltiger Vorgänge, also der acht Verschwendungsarten. Sie stellen das größte Verlustpotential in den Arbeitsprozessen dar.
Der genaue Zusammenhang zwischen den drei Mu’s und mögliche Abstellmaßnahmen aus dem Lean Management sind im nachfolgenden Bild dargestellt.
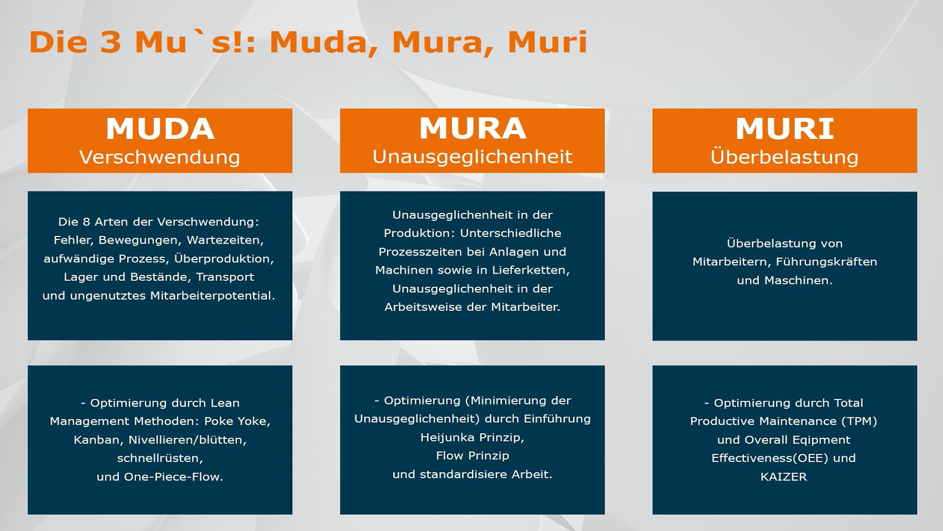
Fokussierung auf Wertschöpfung
Arbeitsprozesse lassen sich generell in zwei Kategorien einteilen. Zum einen in wertschöpfende Prozesse und zum anderen in Verschwendung. Als Verschwendung bezeichnet man alles, was nicht direkt dem Produkt oder dessen Nutzen dient.
Dies bedeutet, dass alle Aktivitäten, die keine Werte schaffen, als Verschwendung zu sehen sind. Dazu gehören alle Funktionen, die vom Kunden nicht genutzt werden und alle Tätigkeiten, die nicht direkt zum Herstellprozess gehören. Anders ausgedrückt setzt sich die gegenwärtige Prozesskapazität aus wertschöpfenden Arbeitsprozessen und Verschwendung zusammen. Um die Effizienz und Produktivität zu erhöhen, muss die Verschwendung identifiziert und möglichst beseitigt werden.
Untersuchungen und Erfahrungen aus der Praxis zeigen, dass der Wertschöpfungsanteil der Arbeitsprozesse in der Regel unter 10% liegt. Bezogen auf die gesamte Durchlaufzeit eines Produktes kann die Wertschöpfung auch unter 1% liegen. Wichtig ist, dass alle Prozesse in einem Unternehmen in Bezug auf ihren Wertschöpfungsanteil gleich klassifiziert werden, damit die Vergleichbarkeit sichergestellt werden kann.
Der Zusammenhang zwischen Wertschöpfung und Verschwendung ist im nächsten Bild dargestellt.
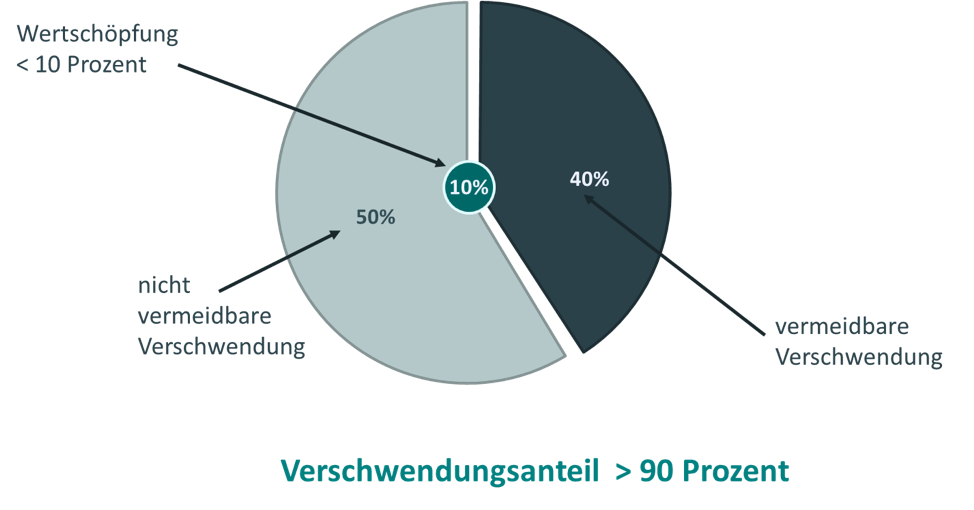
Etwa 50% der Arbeitsprozesse im Unternehmen gelten als „nicht vermeidbare Verschwendung“ und bezeichnen die so genannten Unterstützungsleistungen. Die restlichen 40% sind die „vermeidbaren Verschwendungen“ also Blind- oder Fehlleistungen, welche in vielen Unternehmen regelmäßig auftreten.
Was sind wertschöpfende Tätigkeiten?
Wertschöpfende Tätigkeiten werden auch Nutzleistungen genannt und sind letztendlich die Leistungen im Unternehmen, für die der Kunde bereit ist, Geld zu zahlen.
Was sind nicht vermeidbare Verschwendungen?
Nicht vermeidbare Verschwendung (Unterstützungsleistung) sind Tätigkeiten, die zwar zur Verrichtung der realen Arbeit getan werden müssen, jedoch nicht direkt zu einer Erhöhung der Wertschöpfung im Unternehmen beitragen.
Was sind vermeidbaren Verschwendungen?
Vermeidbare Verschwendung (Blindleistung, Fehleistung) sind kostensteigernde Tätigkeiten, die Zeit und Ressourcen verschwenden. Diese müssen im Rahmen von Lean Management aufgedeckt und unbedingt reduziert (Fehlleistung) bzw. eliminiert (Blindleistung) werden.
Fehlleistungen resultieren in erster Linie aus den acht Verschwendungsarten und müssen so weit wie möglich beseitigt werden, da sie Kosten und Aufwand verursachen und effiziente Arbeitsprozesse behindern. Bei der Beseitigung der Verschwendung ist es wichtig, die Verschwendung zu entdecken und dann auch nachhaltig abzustellen. Hierfür gibt es im Bereich des Lean Managements verschiedene Methoden, die je nach Anwendungsfall sehr gut eingesetzt werden können.
Blindleistungen sind Routineleistungen, welche keinen Wertzuwachs für den Kunden oder das Unternehmen bringen. Daher sind diese Leistungen wertneutral und ohne Bedeutung. Blindleistungen verursachen Kosten und verbrauchen Ressourcen (Energie, Engagement der Mitarbeiter, Kraft, Zeit). Blindleistungen müssen deshalb unbedingt eliminiert werden.
Der Zusammenhang zwischen Nutzleistung, Unterstützungsleistung, Blindleistung und Fehlleistung bei der Beseitigung der acht Verschwendungsarten zeigt das nächste Bild.
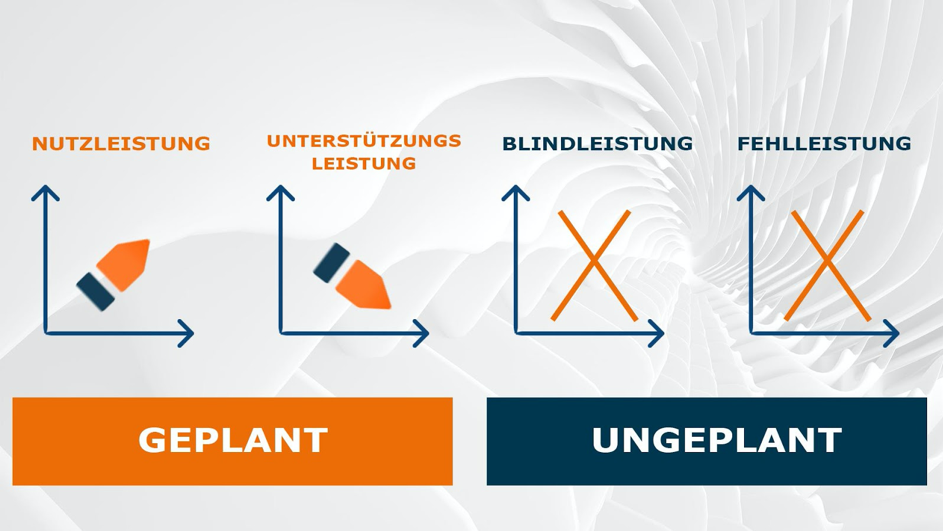
Interessiert an einem fachlichem Austausch oder an einer Beratung?
Schreiben Sie mir gerne eine Nachricht!